Revolutionising the aerospace industry requires innovative approaches that push boundaries and challenge traditional manufacturing methods. With the advent of 3D metallurgy and the power of custom metal powders, a new era of aircraft design and production is unfolding.
By harnessing the potential of additive manufacturing, engineers can now create complex, lightweight structures that were previously impossible to fabricate using conventional techniques. This groundbreaking technology allows for unprecedented geometries, reducing material waste and improving overall aircraft performance.
Incorporating custom metal powders further enhances the capabilities of 3D metallurgy, enabling the production of highly specialised alloys with superior mechanical properties. These powders, tailored to specific requirements, provide manufacturers with the freedom to optimise materials for specific aerospace applications, resulting in lighter, stronger, and more fuel-efficient aircraft.
As the aerospace industry continues to evolve, embracing the power of 3D metallurgy and custom metal powders is not just a trend but a game-changing strategy. By maximising efficiency, reducing costs, and opening up possibilities for groundbreaking designs, this technology is poised to revolutionise the industry in ways we never thought possible.

The role of 3D metallurgy in the aerospace industry
The aerospace industry has long been at the forefront of technological advancements, continuously seeking innovative solutions to enhance aircraft performance, reduce costs, and improve safety. One such revolutionary technology that has gained significant traction in the industry is 3D metallurgy, also known as additive manufacturing (AM) or 3D printing of metal components.
3D metallurgy has transformed the way aerospace manufacturers approach the design and production of aircraft parts and structures. This technology allows for the creation of complex geometries and intricate shapes that were previously impossible or impractical to fabricate using traditional subtractive manufacturing methods. By building up layers of metal powder, 3D metallurgy enables the production of parts with unprecedented levels of customisation, optimisation, and design flexibility.
The ability to create complex, lightweight structures through 3D metallurgy has had a profound impact on the aerospace industry. Engineers can now design parts that are tailored to specific performance requirements, reducing material waste and improving overall aircraft efficiency. This has led to the development of innovative components, such as lightweight engine parts, complex heat exchangers, and intricate aerospace structures, all of which contribute to enhanced aircraft performance, reduced fuel consumption, and improved safety.
Advantages of using custom metal powders in aerospace applications
The success of 3D metallurgy in the aerospace industry is further amplified by the use of custom metal powders. These specialised powders are designed and engineered to meet the specific requirements of aerospace applications, offering a range of advantages over traditional metal alloys.
One of the primary advantages of custom metal powders is the ability to create highly specialised alloys with superior mechanical properties. Aerospace components often operate under extreme conditions, such as high temperatures, high stresses, and harsh environments. By formulating custom metal powders, manufacturers can produce parts with enhanced strength, corrosion resistance, and thermal stability, ensuring the reliability and longevity of aircraft components.
Moreover, custom metal powders allow for the optimisation of material properties to suit the unique demands of different aerospace applications. For instance, engine components may require powders with enhanced heat resistance, while landing gear may necessitate powders with improved fatigue resistance. This level of customisation enables aerospace manufacturers to tailor the material properties to their specific needs, leading to improved overall aircraft performance and efficiency.
The use of custom metal powders in 3D metallurgy also offers significant advantages in terms of manufacturing flexibility and cost-effectiveness. Traditional manufacturing methods often require complex tooling and moulds, which can be time-consuming and expensive to produce. In contrast, 3D metallurgy with custom metal powders allows for the rapid fabrication of parts without the need for extensive tooling, reducing lead times and lowering production costs.
Applications of 3D metallurgy in aerospace manufacturing
The versatility of 3D metallurgy has led to its widespread adoption in various aerospace manufacturing applications, transforming the way aircraft components are designed and produced.
One of the most prominent applications of 3D metallurgy in aerospace is the fabrication of complex engine parts. The intricate geometries and specialised material requirements of engine components make them particularly well-suited for additive manufacturing. 3D metallurgy enables the production of highly optimised turbine blades, impellers, and other engine components with improved aerodynamics, reduced weight, and enhanced performance.
Another area where 3D metallurgy has made a significant impact is the manufacturing of aerospace structures and airframes. The ability to create complex, lightweight, and customised parts has allowed aerospace engineers to design and produce innovative structural components, such as lightweight fuselage sections, wing spars, and landing gear parts. These 3D-printed structures not only contribute to weight reduction but also offer improved structural integrity and enhanced crashworthiness.
3D metallurgy has also found applications in the production of specialised aerospace tools and fixtures. By leveraging the design flexibility of additive manufacturing, aerospace manufacturers can create customised tooling, jigs, and fixtures that optimise the production process, improve efficiency, and reduce lead times. This has led to significant cost savings and increased agility in aerospace manufacturing.
Furthermore, 3D metallurgy has enabled the creation of unique and intricate aerospace components that were previously impossible to fabricate using traditional methods. This includes the production of complex heat exchangers, fuel manifolds, and various other aerospace parts that require intricate internal channels, cavities, and geometries. The ability to design and manufacture these components using 3D metallurgy has contributed to enhanced aircraft performance, improved thermal management, and increased fuel efficiency.
Innovations and developments in custom metal powders for aerospace
As the aerospace industry continues to embrace 3D metallurgy, the development of custom metal powders has become a critical area of focus. Researchers and manufacturers are constantly exploring new formulations and techniques to create specialised powders that meet the unique demands of aerospace applications.
One of the key areas of innovation in custom metal powders is the development of advanced alloy compositions. By combining and tailoring the chemical composition of metal powders, manufacturers can produce parts with enhanced mechanical properties, such as increased strength, improved fatigue resistance, and enhanced thermal stability. This allows for the creation of aerospace components that can withstand the extreme operating conditions encountered in flight.
Another area of innovation in custom metal powders is the incorporation of novel materials and additives. For example, the addition of ceramic particles or reinforcing fibres to metal powders can result in composite materials with improved wear resistance, thermal management capabilities, and structural integrity. These advanced powder formulations enable the production of aerospace parts with unique and enhanced performance characteristics.
Advances in powder production techniques, such as gas atomisation and plasma spheroidisation, have also played a significant role in the development of custom metal powders for aerospace applications. These manufacturing processes allow for the precise control of particle size, shape, and distribution, ensuring consistent powder characteristics that are crucial for reliable 3D metallurgy processes.
Furthermore, the integration of advanced characterisation and analysis techniques, such as X-ray diffraction, scanning electron microscopy, and thermal analysis, has enabled a deeper understanding of the relationship between powder properties and part performance. This knowledge is essential for optimising powder formulations and improving the overall quality and reliability of 3D-printed aerospace components.

Case studies: Successful implementation of 3D metallurgy in aerospace projects
The aerospace industry has witnessed numerous success stories showcasing the transformative impact of 3D metallurgy, highlighting the potential of this technology to revolutionise aircraft design and manufacturing.
The aerospace industry has also witnessed the successful implementation of 3D metallurgy in the production of specialised aerospace tools and fixtures. A major aircraft manufacturer leveraged additive manufacturing to create customised jigs and fixtures for their assembly line, leading to a significant reduction in lead times and increased production efficiency. The ability to rapidly produce these specialised tools using 3D metallurgy has proven to be a game-changer in aerospace manufacturing.
Additionally, the use of 3D metallurgy has enabled the creation of unique and complex aerospace components that were previously impossible to fabricate. A leading aerospace research institute developed a 3D-printed heat exchanger with intricate internal channels for improved thermal management in aircraft. This innovative design, made possible by additive manufacturing, contributed to enhanced engine efficiency and reduced fuel consumption.
These case studies demonstrate the transformative potential of 3D metallurgy in the aerospace industry, showcasing how this technology can drive innovation, improve performance, and enhance the overall efficiency of aircraft design and production.
Importance of partnerships and collaborations in advancing 3D metallurgy in aerospace
The successful implementation and advancement of 3D metallurgy in the aerospace industry rely heavily on fostering partnerships and collaborations. These collaborative efforts are essential in addressing the challenges, driving innovation, and unlocking the full potential of this transformative technology.
One of the key areas where partnerships and collaborations play a crucial role is in the development of custom metal powders. Aerospace manufacturers, material suppliers, and research institutions must work together to formulate and optimise specialised powder compositions that meet the unique requirements of aerospace applications. This collaborative approach ensures that the metal powders used in 3D metallurgy processes are tailored to deliver the desired mechanical properties, thermal stability, and overall performance for aerospace components.
Furthermore, partnerships with research institutions and academic institutions play a vital role in pushing the boundaries of 3D metallurgy innovation. These collaborations allow for the exploration of new materials, the development of advanced processing techniques, and the investigation of novel design methodologies. By combining the expertise of aerospace engineers, materials scientists, and additive manufacturing specialists, these partnerships can lead to groundbreaking advancements that transform the aerospace industry.
Collaborative efforts between aerospace manufacturers and regulatory bodies are also essential in ensuring the safety and reliability of 3D-printed aerospace components. By working closely with organisations responsible for aerospace certification and standards, manufacturers can establish robust quality control protocols, develop appropriate testing and inspection methods, and ensure that 3D-printed parts meet the stringent requirements of the industry.
In the pursuit of advancing 3D metallurgy in the aerospace industry, the importance of fostering a collaborative ecosystem cannot be overstated. By leveraging the collective knowledge, resources, and expertise of various stakeholders, the aerospace industry can overcome challenges, accelerate innovation, and unlock the full transformative potential of this game-changing technology.
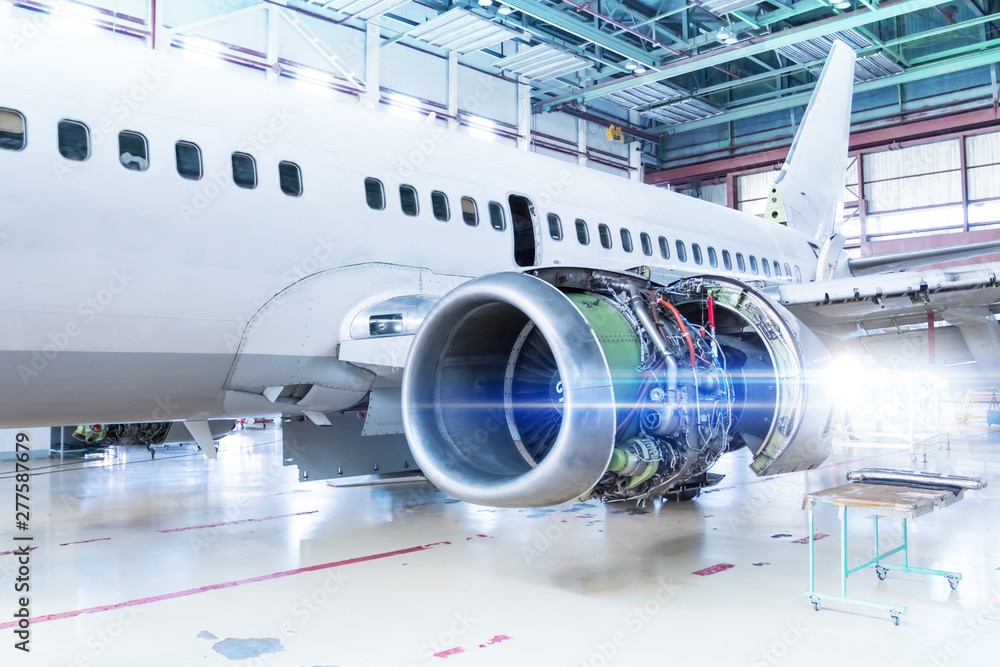
Conclusion: The transformative potential of 3D metallurgy in the aerospace industry
The aerospace industry is on the cusp of a revolutionary transformation, driven by the power of 3D metallurgy and the versatility of custom metal powders. This groundbreaking technology has the potential to redefine the way aircraft are designed, manufactured, and maintained, paving the way for a future where innovation and efficiency are the cornerstones of the industry.
By harnessing the design flexibility and material optimisation capabilities of 3D metallurgy, aerospace engineers can create complex, lightweight, and highly specialised components that were previously unattainable. From intricate engine parts to innovative structural elements, the ability to 3D-print metal parts with customised properties has opened up a world of possibilities for the aerospace industry.
The integration of custom metal powders further enhances the capabilities of 3D metallurgy, enabling the production of highly specialised alloys tailored to the unique demands of aerospace applications. This level of material customisation allows for the creation of parts with enhanced mechanical properties, improved thermal management, and increased overall performance, ultimately contributing to the development of more efficient, safer, and environmentally friendly aircraft.
While challenges and limitations still exist, the aerospace industry is poised to overcome these obstacles through collaborative efforts and continuous innovation. Partnerships between manufacturers, material suppliers, research institutions, and regulatory bodies will be crucial in driving the advancement of 3D metallurgy and ensuring its seamless integration into the aerospace manufacturing ecosystem.
As the industry continues to embrace this transformative technology, the future of aerospace design and production holds immense promise. 3D metallurgy and custom metal powders are set to revolutionise the industry, ushering in a new era of aircraft that are lighter, stronger, and more efficient than ever before. By leveraging the power of this groundbreaking technology, the aerospace industry can soar to new heights, redefining the boundaries of what is possible and paving the way for a more sustainable and innovative future.

How to choose the right metal powder for your business
Choosing the right metal powder for your business is a critical decision that can have a significant impact on the success of your 3D metallurgy projects. To make an informed choice, it’s essential to consider a range of factors, including the intended application. We can help you through this process by explaining the material properties and the manufacturing process requirements, so you get the appropriate powder for your project.
By taking the time to thoroughly evaluate your specific needs and the available metal powder options, we can ensure that you select the most appropriate material for your business, ultimately leading to higher-quality products, improved efficiency, and a stronger competitive edge in the market.
Call our team today on 01642 382000, email gmp@globusmetalpowders.com or complete the contact form on our website for more information.