Be amazed as we unveil the incredible power of Alloy-X metal powder, a game-changer in the industry. With a unique composition of molybdenum and tungsten, this extraordinary alloy redefines the standards of strength and durability.
Alloy-X is the result of years of intensive research and development, unlocking unprecedented performance characteristics. Renowned for its exceptional resistance to extreme temperatures, corrosion, and mechanical stress, this advanced material is in a league of its own.
Whether you’re in aerospace, automotive, or any other field that demands reliability and longevity in extreme environments, Alloy-X has got your back. Its impressive combination of properties makes it ideal for applications where traditional materials fall short.
In this article, we will delve into the fascinating world of Alloy-X and uncover its immense capabilities. From its manufacturing process to its outstanding performance in real-world applications, we will explore every aspect of this extraordinary metal powder. Brace yourself for a journey that will showcase the power and potential of molybdenum and tungsten like never before.
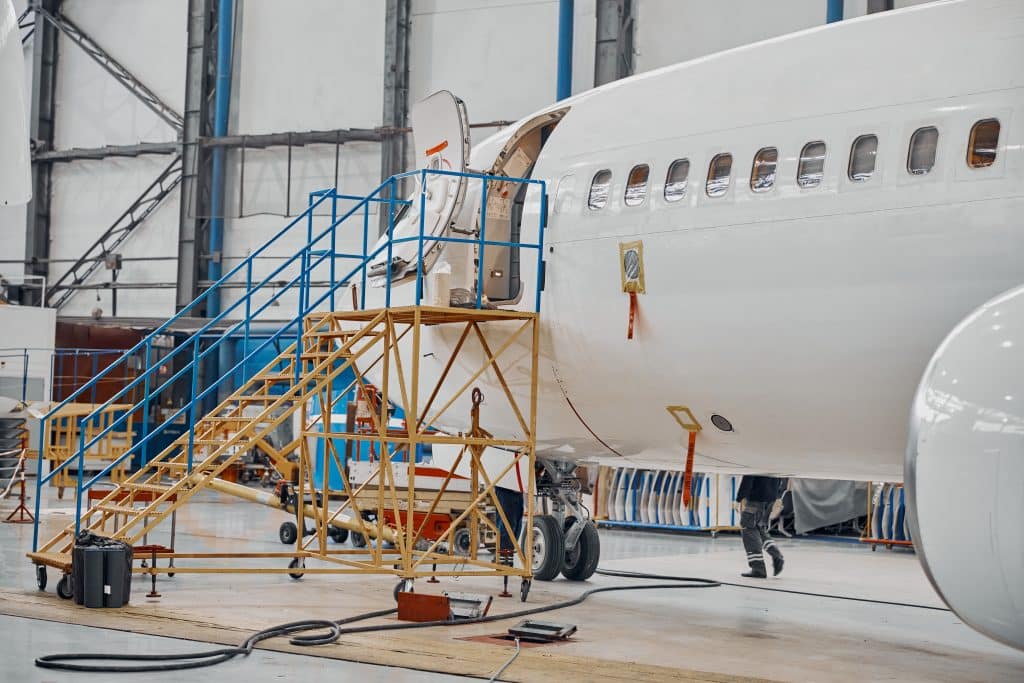
Understanding the properties of Molybdenum and Tungsten
Molybdenum and tungsten are two transition metals that stand out due to their remarkable physical and chemical properties. Molybdenum, with an atomic number of 42, is known for its high melting point of 2,623°C, making it one of the most heat-resistant metals available. Its excellent thermal conductivity and low thermal expansion coefficient contribute significantly to its utility in high-temperature applications. Molybdenum’s excellent resistance to corrosion and oxidation allows it to perform well in harsh environments, ensuring longevity and reliability. This unique combination of attributes makes it a critical component in various alloys, especially those requiring exceptional strength and durability.
On the other hand, tungsten, with an atomic number of 74, boasts the highest melting point of all metals, reaching an astonishing 3,422°C. This property allows tungsten to maintain its integrity under extreme heat, making it indispensable for applications in the aerospace and military sectors. Tungsten also exhibits excellent tensile strength, which means it can withstand high levels of stress without deforming. Additionally, it has a high density, which, when combined with its toughness, makes it an ideal candidate for applications requiring heavy-duty performance. Together, molybdenum and tungsten create a synergistic effect in alloys, enhancing their overall performance and expanding their applicability.
The interaction between molybdenum and tungsten in Alloy-X is a testament to their complementary properties. Combining these two elements results in a metal powder that not only excels in high-temperature performance but also demonstrates exceptional resistance to wear and tear. This unique alloy leverages the strengths of both metals, offering users an unprecedented level of durability and mechanical resilience. As industries continue to encounter increasingly demanding operational conditions, the properties of molybdenum and tungsten become even more critical, underscoring the need for advanced materials like Alloy-X that can meet these challenges head-on.
The benefits of Alloy-X Metal Powder
Alloy-X metal powder stands out in the metallurgy landscape due to its multifaceted benefits, primarily derived from its unique composition of molybdenum and tungsten. One of the most notable advantages of Alloy-X is its superior mechanical strength. The alloy exhibits a remarkable ability to withstand extreme stresses and strains, which is crucial in applications that require materials to perform reliably under intense conditions. This intrinsic strength translates into enhanced performance, reduced maintenance needs, and overall longer service life, making it a preferred choice for industries where reliability is non-negotiable.
Another significant benefit of Alloy-X is its exceptional resistance to high temperatures. Unlike traditional materials that may degrade or lose their structural integrity when exposed to extreme heat, Alloy-X maintains its properties, allowing it to be used in environments where other materials would fail. This characteristic is particularly important in sectors like aerospace and automotive, where components are subjected to considerable thermal stress. The ability to perform consistently in such conditions not only improves safety but also contributes to the efficiency and longevity of the systems where Alloy-X is utilised.
Corrosion resistance is yet another advantage of Alloy-X metal powder. The combination of molybdenum and tungsten provides an impressive barrier against various forms of corrosion, including oxidation and sulfidation. This makes Alloy-X an ideal candidate for applications in chemical processing, marine environments, and other corrosive settings. The prolonged lifespan of components made from Alloy-X not only enhances performance but also translates to significant cost savings over time, as the need for replacements and repairs is greatly diminished. Overall, the benefits of Alloy-X make it a transformative material poised to redefine standards across numerous industries.
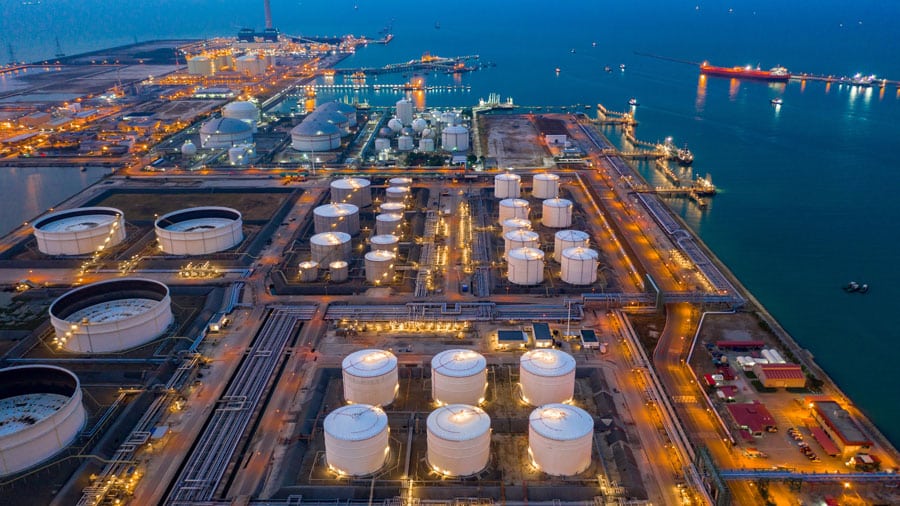
Applications of Alloy-X Metal Powder in various industries
The versatility of Alloy-X metal powder opens the door to a wide range of applications across various industries, each benefiting from its unique properties. In the aerospace sector, Alloy-X is increasingly being adopted for components such as turbine blades and structural parts that are subjected to high temperatures and mechanical stress. Its ability to maintain strength and stability at extreme temperatures ensures the safety and efficiency of aircraft, making it indispensable in a field where performance and reliability are paramount. The lightweight nature of Alloy-X also contributes to fuel efficiency, a critical factor in modern aerospace engineering.
The automotive industry is another area where Alloy-X shines, particularly in the production of high-performance components. Parts such as exhaust systems, turbochargers, and engine components benefit significantly from the durability and heat resistance that Alloy-X offers. As vehicles become more sophisticated and efficient, the demand for materials that can withstand higher temperatures and provide enhanced performance has become essential. Alloy-X meets these demands, allowing automotive manufacturers to produce vehicles that are not only powerful but also reliable and long-lasting, resulting in enhanced customer satisfaction and reduced warranty costs.
In the field of energy production, particularly within the oil and gas industry, Alloy-X metal powder is utilised in drilling equipment and components exposed to harsh conditions. Its superior resistance to corrosion and wear ensures that equipment remains functional and safe over extended periods, even in challenging environments. Moreover, the energy sector often requires materials that can withstand significant mechanical stress, especially during extraction and processing operations. The robustness of Alloy-X not only improves operational efficiency but also enhances safety, minimising the risk of equipment failure and operational downtime, which is critical in this high-stakes industry.
Alloy-X Metal Powder vs traditional materials
When comparing Alloy-X metal powder to traditional materials, the advantages become abundantly clear. Traditional metals, such as carbon steel and aluminium, while effective in many applications, often exhibit limitations when subjected to extreme conditions. For instance, carbon steel, although strong, is prone to oxidation and corrosion, leading to premature failure in harsh environments. Aluminium, while lightweight and resistant to corrosion, cannot withstand high temperatures as effectively as Alloy-X. In scenarios where both strength and durability are essential, Alloy-X emerges as the superior choice, ensuring that components perform reliably over time.
Another area where Alloy-X excels is in its weight-to-strength ratio. Traditional materials may offer adequate strength; however, they often come with added weight, which can be a disadvantage in applications like aerospace and automotive engineering where every gram counts. Alloy-X, with its unique composition, achieves a remarkable balance between strength and weight, allowing for the production of lighter components without sacrificing durability. This characteristic enhances fuel efficiency in vehicles and aircraft, aligning with modern demands for sustainability and performance optimization.
Furthermore, the longevity of Alloy-X metal powder significantly outperforms that of traditional materials. Components made from Alloy-X experience less wear and tear, leading to extended service intervals and reduced maintenance costs. In industries where downtime can lead to substantial financial loss, the durability of Alloy-X becomes a critical factor in decision-making. Traditional materials often require frequent replacements or repairs, leading to increased operational costs and potential safety risks. In contrast, investing in Alloy-X translates to long-term savings and improved operational efficiency, making it a smart choice for industries that prioritise performance and reliability.
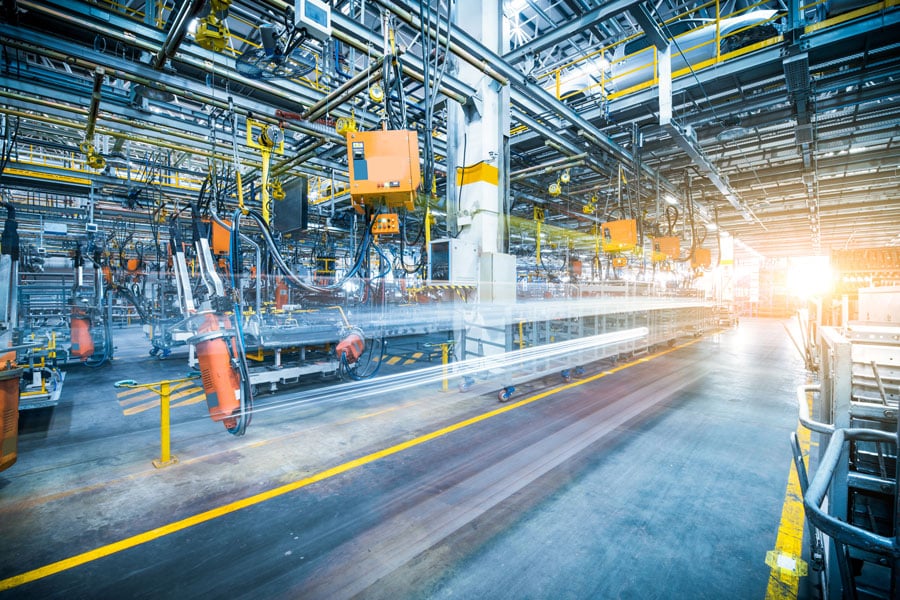
The manufacturing process of Alloy-X Metal Powder
The manufacturing process of Alloy-X metal powder is a sophisticated procedure that ensures the production of high-quality material capable of meeting rigorous industrial standards. The process typically begins with the selection of high-purity molybdenum and tungsten, which are essential for achieving the desired performance characteristics. These raw materials undergo a series of purification steps to remove impurities that could affect the final product’s properties. This meticulous preparation is crucial, as even minor contaminants can compromise the strength and durability of Alloy-X.
Once the raw materials are purified, they are subjected to a powder metallurgy process. This involves the mechanical milling of molybdenum and tungsten into fine powders, which allows for uniform distribution and optimal particle size. The milling process is carefully controlled to achieve the desired particle morphology, ensuring the powder has the right characteristics for subsequent compaction and sintering. After milling, the powders are mixed in precise proportions, tailored to the specific application requirements, resulting in a homogenous alloy powder that maximises the beneficial properties of both elements.
The final steps in the manufacturing process involve compaction and sintering. The mixed powder is pressed into shape using high-pressure techniques, forming green bodies that retain the desired geometries. These green bodies are then subjected to sintering, a process that involves heating the material to a temperature just below the melting point, allowing the particles to bond together without fully melting. This step is critical for enhancing the mechanical properties of the alloy, resulting in a dense, durable material ready for various applications. The careful control of each stage in the manufacturing process ensures that Alloy-X metal powder consistently meets the high-performance standards required across industries.
Testing and quality control of Alloy-X Metal Powder
Quality control is an integral part of the manufacturing process for Alloy-X metal powder, ensuring that the final product meets stringent industry standards. Testing begins with the raw materials, where rigorous assessments are conducted to verify their purity and composition. Techniques such as X-ray fluorescence (XRF) and scanning electron microscopy (SEM) are employed to analyse the elemental makeup and particle morphology of the powders. This initial quality check is vital, as the performance characteristics of Alloy-X are heavily influenced by the quality of its constituent materials.
Once the powder is produced, comprehensive testing is carried out to evaluate its physical and mechanical properties. Common tests include density measurement, flowability analysis, and particle size distribution assessments. These testing methods provide insights into the powder’s behaviour during processing, which is crucial for applications requiring precise specifications. Additionally, mechanical tests such as tensile strength, hardness, and fatigue resistance are performed to ensure that the alloy can withstand the demands of its intended applications. The results of these tests inform adjustments in the manufacturing process, allowing for continuous improvement and optimization.
In addition to physical and mechanical testing, Alloy-X metal powder undergoes rigorous performance evaluations in simulated operational conditions. This step often includes high-temperature and corrosion resistance tests, which are critical for applications in the aerospace, automotive, and energy sectors. The data gathered from these evaluations not only confirms the alloy’s capabilities but also serves as a valuable resource for end-users looking to understand how Alloy-X will perform in real-world scenarios. By adhering to strict testing and quality control protocols, manufacturers ensure that Alloy-X metal powder consistently delivers the reliability and performance expected by industries that demand the best.
Cost-effectiveness and long-term savings with Alloy-X Metal Powder
Investing in Alloy-X metal powder may initially appear to be a higher expenditure compared to traditional materials; however, the long-term savings and cost-effectiveness it provides quickly outweigh the upfront costs. One of the primary factors contributing to this cost-effectiveness is the durability and longevity of Alloy-X. Components manufactured from this advanced material tend to have longer service lives, reducing the frequency of replacements and repairs. This not only translates to fewer disruptions in operations but also minimises the costs associated with downtime, maintenance, and labour.
Additionally, Alloy-X‘s superior performance in extreme conditions leads to increased efficiency in various applications. For instance, in the aerospace industry, the lightweight nature of Alloy-X contributes to enhanced fuel efficiency, leading to significant savings in operating costs over time. Similarly, in the automotive sector, the durability of Alloy-X components means that vehicles can operate optimally for longer durations, resulting in lower maintenance expenses and improved customer satisfaction. The enhanced performance of Alloy-X ultimately contributes to a more economical operation, making it an attractive choice for manufacturers looking to maximise their return on investment.
Moreover, the ability of Alloy-X to outperform traditional materials in terms of strength and resistance to wear means that industries can rely on fewer materials to achieve the same or better performance. This reduction in material usage not only lowers costs but also contributes to a more sustainable manufacturing process. As industries increasingly focus on sustainability and reducing waste, Alloy-X metal powder emerges as a smart choice that aligns with these objectives. By investing in Alloy-X, companies can achieve a balance between performance, cost savings, and environmental responsibility, making it a forward-thinking solution in today’s competitive landscape.
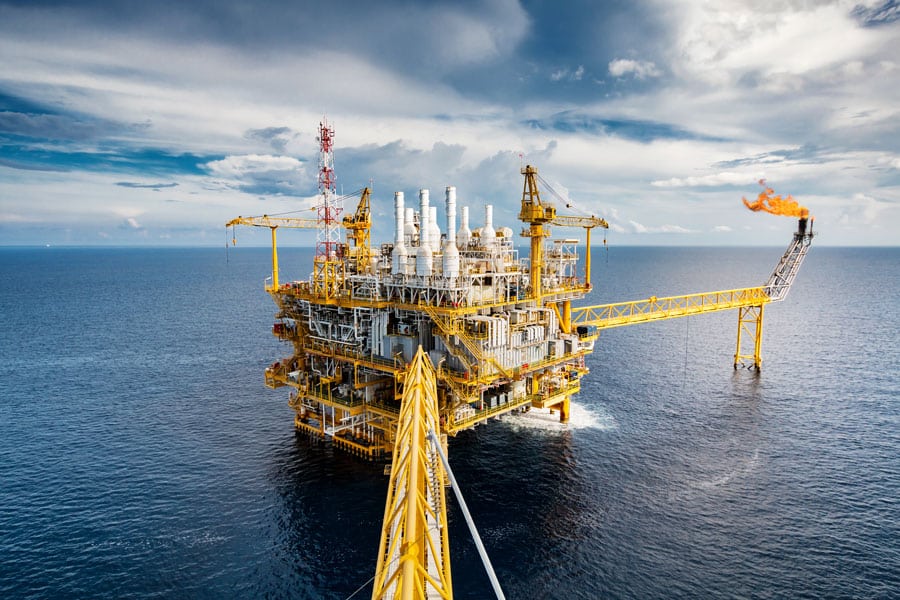
Future developments and advancements in Alloy-X Metal Powder
The field of metallurgy is ever-evolving, and Alloy-X metal powder is at the forefront of this innovation. Researchers and engineers are continually exploring new methodologies to enhance the properties of Alloy-X, aiming to push the boundaries of what this advanced material can achieve. One area of focus is the optimization of the manufacturing process, where advancements in additive manufacturing and 3D printing technologies are being integrated. These innovations allow for the creation of complex geometries and designs that were previously unattainable with traditional manufacturing methods, opening up new possibilities for applications across various industries.
Furthermore, ongoing research is dedicated to understanding the behaviour of Alloy-X under different environmental conditions. By conducting extensive experiments and simulations, scientists aim to uncover new insights into the alloy’s performance, particularly in extreme environments. This research not only aids in the development of new applications but also contributes to the refinement of existing processes, ensuring that Alloy-X remains a leading choice for high-performance materials. The collaborative efforts between academia and industry in this area signify a commitment to advancing Alloy-X’s capabilities and expanding its market reach.
Lastly, the future of Alloy-X metal powder will likely see a growing emphasis on sustainability and eco-friendliness. As industries become more aware of their environmental impact, the demand for materials that not only perform well but also contribute to sustainable practices is increasing. Researchers are exploring ways to enhance the recyclability of Alloy-X and reduce the environmental footprint of its production. By focusing on sustainable development, Alloy-X can position itself as a material of choice for industries that prioritise ecological responsibility alongside performance, ensuring its relevance and importance in the years to come.
Conclusion: Embracing the strength and durability of Alloy-X Metal Powder
In conclusion, Alloy-X metal powder represents a significant advancement in materials science, thanks to its unique composition of molybdenum and tungsten. This innovative alloy offers unparalleled strength, durability, and resistance to extreme conditions, making it an ideal choice for a myriad of applications across industries such as aerospace, automotive, and energy production. The impressive performance characteristics of Alloy-X not only enhance operational efficiency but also contribute to long-term savings, ensuring that companies can achieve their goals without compromising on quality or reliability.
As we look toward the future, the potential for Alloy-X continues to expand, driven by ongoing research and advancements in manufacturing technologies. The integration of additive manufacturing and a focus on sustainability will likely revolutionise how Alloy-X is produced and utilised, allowing for even greater versatility and applicability. Industries that embrace Alloy-X will be well-equipped to navigate the challenges of modern engineering, leveraging its strengths to create innovative solutions that meet the demands of an ever-evolving market.
Ultimately, the power of Alloy-X metal powder lies in its ability to redefine the standards of strength and durability in materials. By choosing Alloy-X, manufacturers and engineers can ensure that their products are built to last, providing peace of mind and confidence in performance. As we continue to explore the capabilities of this remarkable material, the future looks bright for Alloy-X and the industries that harness its potential. Embrace the strength and durability of Alloy-X metal powder and unlock new possibilities for innovation and excellence in your projects.
How to choose the right metal powder for your business
Choosing the right metal powder for your business is a critical decision that can have a significant impact on the success of your 3D metallurgy projects. To make an informed choice, it’s essential to consider a range of factors, including the intended application, we can help you through this process by explaining the material properties and the manufacturing process requirements, so you get the appropriate powder for your project.
By taking the time to thoroughly evaluate your specific needs and the available metal powder options, we can ensure that you select the most appropriate material for your business, ultimately leading to higher-quality products, improved efficiency, and a stronger competitive edge in the market.
Call our team today on 01642 929130, email gmp@globusmetalpowders.com or complete the contact form on our website for more information.